Home › Laboratory › Furnaces, Ovens & Incubators › Nabertherm
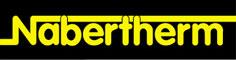
Gas Supply Systems/Vacuum Operation for Tube Furnaces RS, RHTC, RHTH and RHTV

|
When equipped with various equipment packages, the tube furnace series RS, RHTH, and RHTV can be adapted for operation with nonflammable or flammable gasses or for vacuum operation. The different equipment packages can be delivered together with the furnace, or later as needed.
Gas Supply System 1 for simple protective gas applications (no vacuum operation)
This package represents a basic version sufficient for many applications, for operation with nonflammable protective gasses. The standard working tube made of ceramic C 530 delivered with the furnace can still be used.
Working tube of ceramic C 530 can be used 2 plugs of ceramic fibre with protective gas connections Gas supply system for nonflammable protective gas (Ar, N2, forming gas) with shutoff valve and flow meter with control valve (volume 50-500 l/hr), piped and ready to connect (gas intake pressure at 300 mbar to be provided by customer)
Additional Equipment
Extension of gas supply system with a second or third nonflammable type of gas Bottle pressure regulator for use with bottled gas Automatically controlled gas supply with solenoid valves on the gas supply panel, which can be switched on and off through a controller with programmable extra functions (e.g. P 320)
|
 |
Gas Supply System 2 for gas-tight operation with nonflammable gasses/vacuum operation
For increased atmospheric purity requirements in the working tube, we recommend this gas supply system. The standard working tube is replaced by a dense working tube of ceramic C 610 or C 799 in a gas-tight design. Besides the longer working tube, the scope of delivery also includes gas-tight flanges and a corresponding bracket system in the furnace. The system can also be equipped for vacuum operation.
Longer, gas-tight working tube of ceramic C 610 for furnaces to 1300 °C or of C 799 for temperatures above 1300 °C
2 vacuum-tight, water-cooled stainless steel flanges with fittings on the outlet side (cooling water supply with NW9 hose connector to be provided by the customer)
Mounting system on furnace for the flanges
Gas supply system for nonflammable protective gas (Ar, N2, forming gas) with shutoff valve and flow meter with control valve (volume 50-500 l/hr), piped and ready to connect (gas intake pressure at 300 mbar to be provided by customer)
Additional Equipment
Extension of gas supply system with a second or third nonflammable type of gas
Bottle pressure regulator for use with bottled gas
Automatically controlled gas supply with solenoid valves on the gas supply panel, which can be switched on and off through a controller with programmable extra functions (e.g. P 320)
Water-cooled end flange with quick connectors
Cooling unit for closed loop water circuit
Vacuum Operation
Vacuum package for evacuation of the working tube, consisting of a tee for the gas outlet, 2 ball valves, manometer, 1-stage manually operated rotary vane vacuum pump with corrugated stainless steel hose connected to the gas outlet, max. attainable end pressure in working tube about 10-3 mbar
|
Gas Supply System 3 for gas-tight operation with hydrogen, introduced above 800 °C/vacuum operation
Adding gas supply system 3 to the tube furnace allows operation under a hydrogen atmosphere. The built-in safety system allows the introduction of hydrogen into the working tube, when heated to at least 800 °C. The furnace and control system are designed to provide the highest possible degree of safety for the furnace, operator, and surroundings.
Longer, gas-tight working tube of ceramic C 630 for furnaces to 1300 °C, or of C 799 for temperatures above 1300 °C2 vacuum-tight, water-cooled stainless steel flanges with fittings on the outlet side with cooling water supply (to be provided by the customer) and NW9 hose connector
Mounting system on furnace for the flangesSafety system for gassing with flammable protective gases starting at 800 °C
Exhaust gas torch, propane-powered for customer-installed propane gas supply at 30 mbar
Gas supply system for H2 and N2. The customer provides an H2 supply at 300 mbar
and a N2 supply at 10 bar
N2 emergency purge container
PLC-controlled regulation with operation via HiProSystem touchscreen, locking procedures, and safety matrix programmed into the software
Tube furnace RHTH 70/600/18 with gas
Additional Equipment
Extension of gas supply system with a second or third nonflammable type of gas
Bottle pressure regulator for use with bottled gas
Cooling unit for closed loop water circuit
Vacuum Operation
Vacuum package for pre-evacuation of the working tube, consisting of a tee for the gas outlet, 2 ball valves, manometer, 1-stage manually operated rotary vane vacuum pump with corrugated stainless steel hose connected to the gas outlet, max. attainable end pressure in working tube about 10-3 mbar
Vacuum package with adapted pumps for a max. end pressure down to 10-5 mbar upon request (see below)
Gas Supply System 4 for gas-tight operation with hydrogen, introduced at room temperature/vacuum operation
Adding gas supply system 4 to the tube furnace allows operation under a hydrogen atmosphere. The built-in safety system allows the introduction of hydrogen into the working tube at room temperature. The furnace and control system are designed to provide the highest possible degree of safety for the furnace, operator, and surroundings.
Equipment as for gassing package 3, but with extended safety system for operation with hydrogen at room temperature.

Tube furnace RHTH 70/600/18 with gas supply system 4 |
 |
Vacuum Pumps
With respect to the final pressure different pumps are available:
Single-step rotary piston pump for a max. final pressure of approx. 20 mbar.
Two-step rotary piston pump for a max. final pressure of approx. 10-2 mbar.
Pump system PT70 Dry (rotary vane pump with following turbomolecular pump for a max. final pressure of 10-5 mbar.
Information
For protection of the vacuum pump only cold stage evacuation is allowed. The reduction of working tube
strengthness limits the max. possible working temperature under vacuum.
Please note - Product designs and specifications are subject to change without notice. The user is responsible for determining the suitability of this product.
|