The compact furnaces of the VHT line are available as electrically heated chamber furnaces with graphite, molybdenum or MoSi2 heating. A wide variety of heating designs as well as a complete range of accessories allow optimal furnace configuration for technically demanding customer processes.
The vacuum-tight retort enables heat treatment processes either in protective and reaction gas atmospheres or in a vacuum, depending on the application, all the way to 10-5 mbar.
With the appropriate safety technology, the furnaces are also suitable for operation with hydrogen.
Heating Concepts
Graphite VHT ../GR
Suitable for processes under protective and reaction gases or under vacuumTmax 1800 °C and 2200 °CGraphite felt insulationTemperature measurement using type B thermocouple (version to 1800 °C)Temperature measurement using optical pyrometer (version to 2200 °C)
Molybdenum VHT ../MO
Suitable for processes under highly pure protective and reaction gases or under a high vacuum up as much as 10-5 mbar Tmax 1600°C Insulation made of Molybdenum steel sheets
MoSi2 VHT ../KE
Suitable for processes under protective and reaction gases, under vacuum or in air
Tmax 1800°CInsulation made of high purity aluminum oxide fiber
|
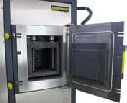
Graphite heating chamber
|
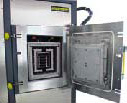
Molybdenum heating chamber
|
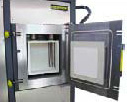
Chamber made of ceramic fibre
|
|
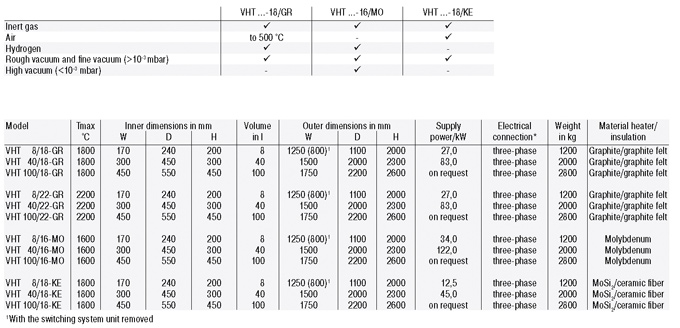
Models in this range include the VHT 8/18, VHT 40/18, VHT 100/18, VHT 8/22, VHT 40/22, VHT 100/22, VHT 8/16, VHT 40/16, VHT 100/16, VHT 8/18, VHT 40/18 and VHT 100/18.
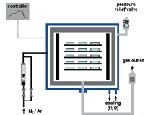

The use of automatic valves for process gas or exhaust air management and the powerful H3700 controller allow the entire heat treatment process to be run fully automatically. The entry of all process data (temperatures, ramps, gas supply and vacuum) is easily controllable from a large, 12" graphic control panel. System status with all process-related data are clearly shown on a process control diagram. All valves and the vacuum pump can also be operated manually from here as well.
The system has an automatic pre-program and post-program for purging the furnace chamber and also features automated leak testing.
Automatic Version VHT without Hydrogen Operation
Features the same as basic version of VHT, plus:
Automatic gas supply for one process gas (N2 or Ar) with adjustable flow
Bypass for rapid filling or flooding of furnace chamber
Automatic gas outlet with check valve and pressure relief valve (20 mbar)
Single-stage rotary vane pump with check valve for pre-evacuating and heat treatment in a rough vacuum to 20 mbar
Transducer for absolute and relative pressure measurements
H3700 controller (10 programs with 20 segments each)
Operation with 12“ graphical control panel (touchpanel)
Additional Equipment
Mass flow controller for varying flow volumes and generating gas mixtures (with second process gas)
Furnace pressure control with position-controlled exhaust valve (partial pressure control)
Electric or gas-heated exhaust gas torch for process gas post-combustion
Water-cooled exhaust gas cooler
Condensate traps for separation of large amounts of binder
Two-stage rotary vane pump with check valve for pre-evacuating and heat treatment in a vacuum to 10-2 mbar
Pump stand with turbo-molecular pump and slide valve for pre-evacuating and for heat treatment in a vacuum to 10-5 mbar (only for molybdenum model) including electric pressure transducer and booster pump
PC control via NCC with enhanced optional documentation and possible connection to customer LAN
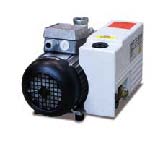 |
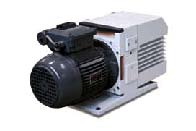 |
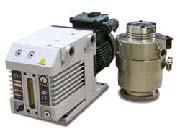 |
Single-stage rotary vane pump for heat treatment in a rough vacuum to 20 mbar |
Two-stage rotary vane pump for heat treatment in a vacuum to 10-2 mbar |
Turbo-molecular pump with booster pump for heat treatment in a vacuum to 10-5 mbar |
Extension Package Hydrogen in VHT-MO
When hydrogen is used as a process gas, our systems come equipped with additional safety technology. Only certified and industry proven safety sensors are used. The furnaces are always controlled using a fail-safe controller (S7-300F/safety controller). The controller and documentation are carried out using Nabertherm Control Center NCC.
Two Temperature-Dependent Concepts Available for Safe Operation with Hydrogen:
Partial pressure operation: H2 infeed under controlled negative pressure (partial pressure) in the process reactor starting from 750 °C furnace chamber temperature Atmospheric operation: H2 overpressure infeed in process reactor starting from room temperature
Automatic Version VHT for Operation with Hydrogen
Features as found with automatic version of the VHT without hydrogen operation, plus Redundant process gas valves for hydrogenMonitored pre-pressures of all process gasesBypass for safe flushing of furnace chamber with inert gasPressure-monitored emergency flooding with automated solenoid valve opening element
Electric or gas-heated exhaust gas torch for H2 post-combustion
Extension Package Debinding and Sintering
The "Debinding and Sintering" extension package allows VHT furnaces with molybdenum heating to be used for processes causing process-related contamination during heat treatment. The furnace is equipped with an additional retort with direct gas inlet and outlet and exhaust gas torch.Special gas plumbing prevents contamination of the furnace insulation and the heater due to the thermal process. The furnace can also optionally be equipped with a heated gas exhaust, a partial pressure debinding system, and a binding agent trap. The control system corresponds to that of the "Automatic" extension package.
Automatic Version VHT-MO for Debinding/Sintering
Features such as the automatic version of the VHT without hydrogen, plus: Additional molybdenum retorts in the furnace chamber with direct gas inlet and outlet for protecting the furnace insulation Exhaust gas torch for post-combustion of gases produced by process Exhaust gas cooler
Additional Equipment
Heated gas outletBinding agent trap with condensate separation for processes with a large proportion of binding agentsCooling unit for closed-loop water circuit
Please note - Product designs and specifications are subject to change without notice. The user is responsible for determining the suitability of this product.